澳大利亞科學家開發新型超薄觸碰螢幕材料
撰文者: 塑膠智庫 | 出刊日期:2023-05-12 | 文章編號:HNCH4HQ4YP
993
瀏覽數
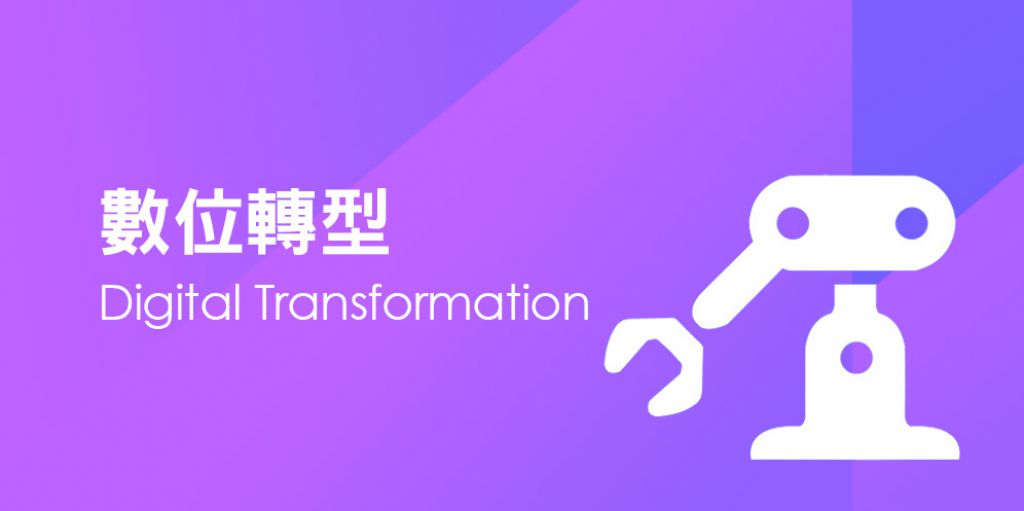
澳大利亞的科學家開發出一種超薄且高度靈活的電子材料,這種材料具有觸碰感應功能,比目前智慧型手機螢幕厚度薄100倍。可以像印刷報紙一樣使用卷對卷(Roll-To-Roll, R2R)處理進行大規模生產。
撰文者: 塑膠智庫 | 出刊日期:2023-05-12 | 文章編號:HNCH4HQ4YP
993
瀏覽數